Product Introduction
The servo drive combines a high-performance motor with a precision feedback system to achieve precise control of the permanent magnet synchronous motor. The drive has real-time feedback and can quickly adjust according to load changes to ensure efficient and stable operation. The servo drive is very suitable for applications that require high dynamic response.
Key highlights
1. Control mode: supports position, speed, and torque control modes, realizes millimeter-level positioning and dynamic path following, and adapts to AGV high-speed obstacle avoidance and flexible grasping.
2. Communication protocol: compatible with CANopen, EtherCAT and other protocols, seamlessly connected to AGV navigation and scheduling systems.
3. Encoder adaptation: fully compatible with photoelectric, magnetic, and absolute encoders to meet high-precision positioning requirements.
4. Motor drive: adapts to 500W~20kW low-voltage servo motors, covering light load to industrial heavy load scenarios.
5. Two-in-one drive (drive + energy management), emergency alarm braking, battery life optimization; supports customized development of working conditions (such as explosion-proof, extreme temperature resistance, and impact resistance).
6. Supporting software: The interface is simple and clear, with 0.1-level accuracy to display voltage, current, DI/DO status, millisecond-level real-time curve tracking instructions and feedback; parameter step adjustment (±1/±10), alarm record loop storage, convenient and accurate debugging.
Application Areas
1. High-precision handling: semiconductor wafer transport AMR, medical laboratory precision instrument handling (±0.1mm positioning).
2. High-speed logistics: e-commerce warehousing sorting AGV (2m/s high-speed operation, 100,000 times/day start-stop life).
3. Complex path scenarios: multi-machine collaborative AMR cluster (360° omnidirectional movement, dynamic obstacle avoidance).
Six quality assurances
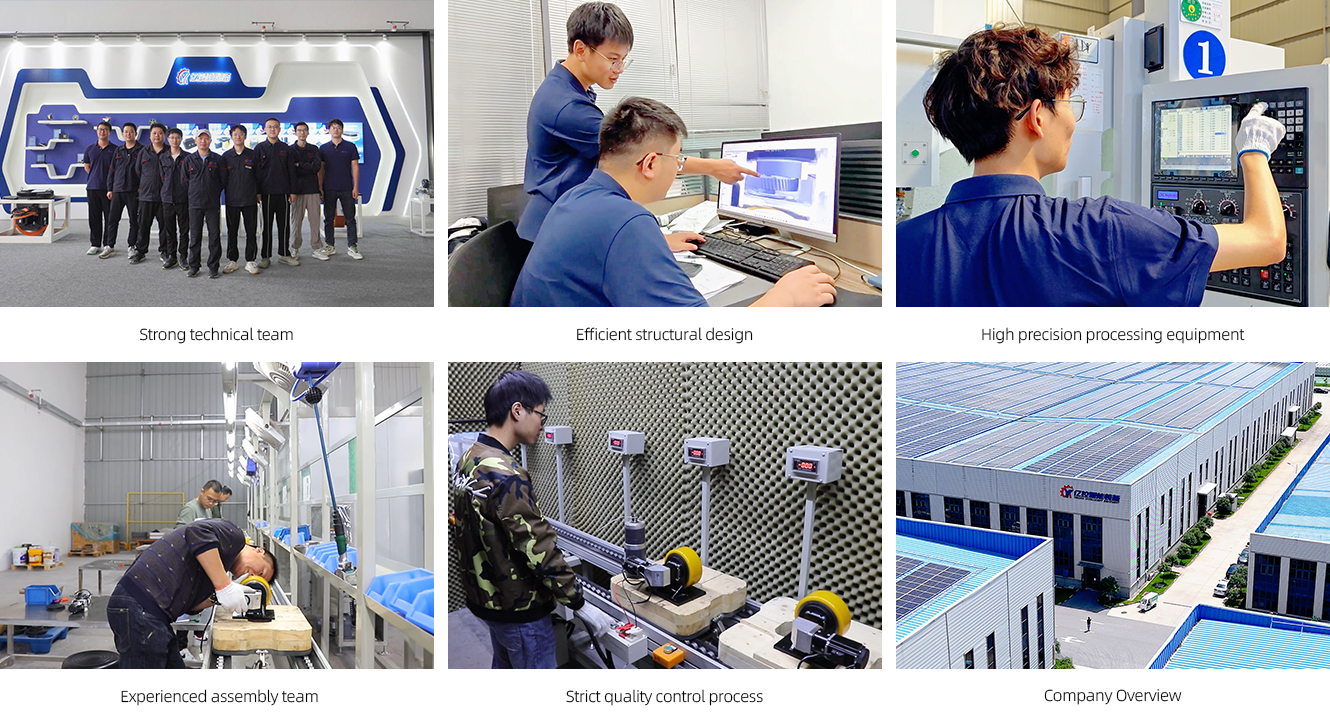
Product parameters (specifications)
基本参数型号 Basic Parameter | TEC-PSH-I-U | TEC-PSM-I-U | TEC-PSL-A-U | TEC-PSS-A-U | TEC-PSS-I-U |
电气参数
Power parameters | 电源电压 Voltage | DC 12-72V |
额定电流 Rated Current | 150A/100A | 50A | 30A | 25A/10A |
控制 Motor controls | 控制方式 Control modes | 1:速度闭环控制 Velocity loop | 1:速度闭环控制 Velocity loop 2:位置闭环控制控制 Position loop |
输入输出接口 I/O interfaces | 模拟量输入 AIs | 1路0 - 10V模拟量 One AI Input,range:0 to 10V |
数字量输入
DIs | 4路数字量输入,低电平有效 Four DIs,active low |
数字量输出 DOs | 2路集电极开路输出,最高耐压30V,最大支持电流1A Two DOs,open-collector,VBR 30V,ID max 1A |
12V输出 12V output | 1路12V电源输出,最大电流200mA One 12V output,maximum Continuous current 200mA |
反馈方式 Feedback | 编码器接口 Encoder | 5V,霍尔+增量,差分输入 5V,Hall+Incremental encoder, differential input | 5V,RS485绝对值/霍尔+增量,差分输入 5V,absolute,RS485 input/Hall+Incremental encoder,differential input |
通讯接口 Communication | USB | USB连接上位机软件 Configuration software,USB interface |
CAN | 标准CANopen协议 CANopen |
FAQ
Servo drives are ideal for applications that require high precision and fast response, such as automated production lines and high-precision machining.
Using the accompanying software tool, the parameters of the servo drive can be easily adjusted to meet specific application requirements.
Servo drives can use encoders, resolvers, or Hall sensors as feedback devices for high-precision position control.